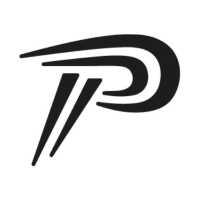
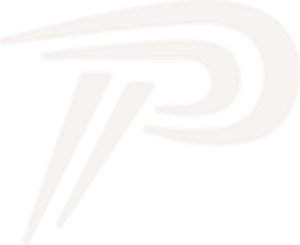
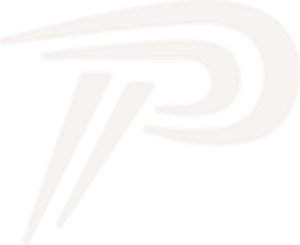
Master Instrument Maker and Repair Person
Bringing instruments back to life and creating dream guitars since 2002.
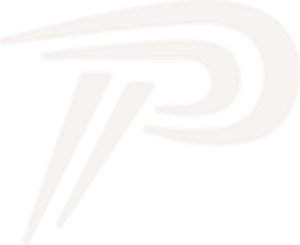
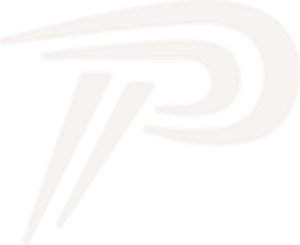
Master Instrument Maker and Repair Person
Bringing instruments back to life and creating dream guitars since 2002.
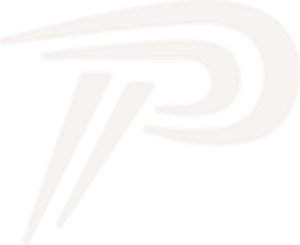
Repair and Servicing Work
We offer a wide range of repair and servicing work.
From the simplest job to the most complex we are here to help you.
Jobs we take on:
Servicing and maintence work - Broken necks repairs or replacements - Vintage restoration work
Component repair or replacement and upgrades - Bespoke parts manufacture - Pickup custom builds and rewinds
All our services come with our expert advice.
We take jobs on by a case by case basis, as your instrument in unique and so is the service we will provide you.
We are proud to produce the highest quality of work and offer our services by appointment only.
By keeping to appointments we ensure fastest turnaround times whilst keeping to the highest standard of work.
We can undertake most everything in house and have numerous trusted suppliers that we work with to make sure we are always giving you the best possible service.
Services and Costs
The price list below will act as a guide to prices as every job is tailored to your requirements and every instrument is different this is a guide to our prices.
Standard Set up and Deluxe Set-up
We offer a Standard Set up and a Deluxe Setup Service, our Set-up services will get you instrument playing at its very best! Firstly we start with a consultation. We check for any issues that may need repairing that would inhibit us from doing a successful setup. The work completed on your guitar will vary due to the components that are used in its construction, I will list the most common adjustments instruments require based upon the two major types of instrument, that of Fender and Gibson and their style of construction.
Adjustments:
The Neck - tension of the truss rod, sets the relief in the neck, very flat for low actions bow for those who enjoy playing the instrument hard.
String Height - at the nut and the bridge, this can either be low medium or high.
String Radius - making sure the strings form a uniform radius that usually increases in height on the bass side of the fretboard, this can be done either individually or by filing the saddle at the bridge.
Intonation - Sets the string length at the bridge to achieve accurate notes upon the fretboard.
These actions set the playability of the instrument and will be defined during the consultation.
Set Pickup Height - Pickup distance from the strings affects the tonal output of the guitar. Pick-up heights vary from one instrument to another and are dependent on a number of factors. Generally the closer you can get to the string the higher the output of the pickup.
The level of work to will be discussed with the customer and we will endeavour to set the instrument up to meet their requirements. We take extra time after completion of the work to make sure you are happy with the end results and are happy to make any necessary final adjustments that are needed
Maintenance and cleaning:
Cleaning the fingerboard - after many years of use the fretboard may have built up a level of detritus, which is dead skin cells and natural oils from sweat that build up over time. We make sure to remove any dirt before the setup process begins.
Most fingerboards are natural oil-bearing timbers, which means they produce their own oil, we use the appropriate amount of fretboard conditioners to help restore or maintain the timber's condition.
Some fingerboards are painted as they are not oil-bearing timbers these are treated like any other painted surface and receive a good cleaning and protection they require.
Polish FretWire - We make sure to use a polish and pads that are safe for use and will not damage the timber or leave behind residue that will damage the timber going into the future.
General maintenance - Cleaning of the guitar making sure it gets a good polish and is nice and clean when it is returned.Upkeep of Electronics - Making sure they are cleaned and lubricated and that parts are tight and forming good connections that maintain a good signal.
Clean and Lubrication - General maintenance and upkeep of parts making sure any corrosion issues are addressed. Deep to light cleaning depending on the grime build-up on the particular instrument.
Lubrication of the tremolo, nut and any other moving parts that require lubrication, always using the correct type of lubrication for that particular part making sure all moving parts receive the right amount of attention to keep them at peak performance.
Deluxe Set up
Everything you will get in the setup with extra time given to every detail to make sure things are as perfect as they can be. Allowing extra time for each activity listed above allows for a tougher job. A complete disassembly and reassembly of the instrument cleaning and lubricating everything as we go making 100% sure that your instrument is ready for its time on the road again! Well worth it for touring musicians whose instruments often suffer on the road and for those who like their instrument upkeep to be top-notch.
Set-up from £65Deluxe Set-up £80-150
Additional costs are involved with setting up floating tremolo units dependeing on the type of system. Usually around £20-30 extra
Acoustic Set-up from £45-65
Acoustic 12 strings from £65
FretStone
Work involved - The frets are leveled and crowned, in most cases removing any signs of wear. The frets will be re-shaped to a uniform shape and height, checking for accuracy during the process.
When you bring your guitars in we will check for any issues the fingerboard may have any high or low frets, any that have become loose and are lifting if there is any twist or warp in the neck and if there is any lift at the end of the fingerboard or S bend. We also look for any issues that may need repairing that would inhibit us from doing the job to the utmost of our ability.
After the instrument has undergone the consultation and checks a final estimated cost can be confirmed as the level of wear will be different for each guitar. Some guitars may require a light fretstone when they are brand new, this is due to high and low frets impeding the potential playability of that instrument. They can leave the factory and not have seen any leveling and corrections making them very difficult to set up without fretting out. This job will be vastly quicker than that of an instrument that has been played a lot and has excessive fret wear so we price each job accordingly.
I am proud to say we do the best fretwork available. When we stone your frets we level several times and make sure we keep to a uniform size and shape and make sure they are 100% level and that the crown shape is as perfect as it can be. Accuracy and passion for our work are the driving forces of our business.
We like to achieve the best actions possible and I am well known for some unbelievably low actions. some fretboards lend themselves to low actions if this is not the case we can tailor the fretboard to give you extremely low actions. A compound radius will give you the lowest action where as a set radius always has issues at the end of the board when the string action is low. By sanding in a compound radius at the end of the fingerboard we can achieve better actions with these instruments, this comes at the cost of note accuracy in the very high register. If you're not bending a note or a vibrato there anyway your doing something wrong! If you are a fan of medium to higher actions then we have you covered, by using our Peterson strobe tuner we are able to set the guitar up to be as accurate across the fingerboards notes as possible this is a great setup for recording so that the notes are as perfect as possible for recording reasons. Hence why studio professionals and recording artists recommend me and use my services.
We have two polishing methods we can either use our pedestal metal buffers or rotary buffers. The pedestal buffer will get you to the highest shine possible although will destroy binding nubs or anything softer than metal. The rotary buffer is the kind of thing that most luthiers use and is much softer than the metal buffing technique, unfortunately, it does not reach the highest gloss levels that we can provide.
All guitars undergoing a fret-stone will require a setup after wards to set the action and make them play at their very best and come back nice and clean with everything working as it should.
Final costs are dependent upon the amount of time the entire job takes, a guide to our pricing is below.
Brand new guitars just require a small tickle to the frets to get them level - from £100
Regular fret stone applicable to most guitars Fret Stone - from £160
Binding Nubs where a more careful polishing method needs to be used - from £160
Stainless steel fret stones take a longer working time, fortunately, usually not that worn down as they resist wear very well - from £180
Re-fretting
Work Undertaken: removal of the old fret wire with as little damage to the timber of the fretboard as possible and replacement with new fret wire, the frets are then leveled, re-crowned and polished to the highest level, using the same procedure as the fretstone. The frets need to match perfectly in shape and height so they are uniform as this helps us achieve the best action and accurate intonation.
Finishing services are available for maple and other painted fingerboards, on an individual job basis.
Fret Materials and differences:
Nickel Steel - Is the most common type of fret wire fitted to most musical instruments, it comes in a range of toughness the higher nickel content will increase the strength of the wire, so we only fit 18% or higher content as standard. A low Nickel content of 12% is only available upon request.
Stainless Steel - This is a much harder version of fret wire than the standard Nickel Steel. It is a tougher material to work with requiring more time installing and shaping. It is much harder wearing than the standard nickel steel lasting twice if not more longer without the need for maintenance.
We recommend this product for maple necks with a finish applied so that the frets last much longer than standard frets. The extra wear resistance is a good upgrade to have over standard fret wire if the instrument is played a lot and regular maintenance is not possible. It does change the tone making the guitar brighter and sharper transients that are most noticeable on mellow-sounding fretboards like rosewood and ebony, the difference is minor with maple and other trebly types of timber, most of these types of timber have finished fretboards so with very little sound difference and the long-lasting nature of this material lends itself to use with painted fingerboards.
Evo Gold - Nickel-free fret wire that is gold in colour, that is hard-wearing, for anyone who has allergies to nickel and ideal for use on gold hardware guitars so the fret wire matches the gold finish.
Other materials are available upon request - Brass is available for the Warwick and classical instruments. Other materials are available upon request.
Final costs are dependent upon the amount of time the entire job takes a guide to our pricing is below.
Re-Fret Standard - from £320
High-Level Re-Fret
Necessary for re-frets with no fret tang visible, in the case of binding even refrets maintaining fret nubs at the ends of the fret wire - from £400
Painted fingerboard's final costs are dependent upon the amount of time taken estimated cost -from £360
A new bone nut is often needed also and this is something to be aware of. The cost of a new nut is often worked into the final cost of the re-fret for you.
Fretless Bass Conversion
De fret and conversion into a fretless bass with fret slot infilled with timber, resin, plastic or any other material either finished or unfinished dependent on the fingerboard material - from £340
Top Nut Replacement
Materials available - Bone is the classic material for an instrument nut and the most common replacement material we use - Not all bone is equal - there are some very soft bones that you find today on budget instruments. All the bone that we buy is of a good standard!
Different types of bone - Bleached bone, the most common material - Unbleached bone is more yellow in colour that can vary - Argentinian Cow is again yellow in color this bone that ias a very dense material - Camel bone is another dense material that can be very colourful with hints of red if unbleached.
Graphite Nuts - Graphtech produces a large range of TUSQ nuts and saddles these are modern alternatives to bone that are made from self-lubricating materials, either in black or white - it's complicated, there is a large range - There are other companises making graphite nuts also.
Compensated nuts - These are generally made from a similar material to Graphite nuts and allow the nut to be compensated so the bridge saddles follow a straighter line, this is for more accuracy with intonation and the fretted notes. This idea follows micro-fret guitars 1967-1975 now reopened as of 2017 that had adjustable string nuts so the string length can be altered at the nut.Keratin Horn Materials - Water buffalo horn is a dark gray and black striped material that is made of keratin horn material - Mammoth horn is the most expensive material for a nut and is the closet to ivory unless you can bring me an old piano key that we can make a nut out of.
Metal - Brass is a commonly used nut material that is very hard-wearing, it does alter the sound of the instrument, this depends upon the instrument it is fitted to, generally it sounds more like a fretted note that gives you more sustain and body to the sound, bigger booming open notes and extra sustain, brass can be combined with bone to give you a more nuanced sounding nut that still gives you some of the benefits of a full brass nut, some extra sustain and will sound like a fretted note without having the full tone of a brass nut.
Aluminum nuts - exist on some instruments although very rarely fitted.
For most standard guitars we can offer pre-made bone nuts also we work with metal, brass nuts being an occasional request and a lot of materials can be used to make an instrument nut
Plastic / Nylon / Teflon nuts - If a direct type or replacement is preferred usually on a vintage instrument then we do offer plastic, nylon and Teflon nuts as part of our service to keep the originality of the instrument as this is important when it comes to vintage restorations.
Many guitars use plastic nuts, almost all old Japanese guitars have this nut material. Nylon nuts are found on all old Gibson guitars from the golden era, Teflon nut have been around for a long time, modern Teflon nuts materials are much better than the material was when it was first introduced.
We pride ourselves on the accuracy of our nuts with spacing and heights set perfectly, whist others may make you a nut we can talk to you about spacing and any unusual particularities that you would like.
Nut costs vary a lot with their being premade replacement nuts that require very little work when installing to making a bespoke nut from an oversized blank to fill a larger-than-normal nut slot, that one catches me off guard now and then.
Final costs are dependent upon the amount of time the entire job takes a guide to our pricing is below.
Six string nut costs
Worked into another job estimated costs £30-80
Pre-made nuts fitted from £30 to £50
Bespoke nut from £60
12 string nuts £110
Bass nuts
Repair work
Repair work - varies a lot in the scope of the work as no two jobs are alike, so below is a guide to the most common repairs that we encounter and guide prices to help you understand the cost involved.
Broken Neck - come in a variety of severities, sometimes just need some glue and refinishing - sometimes they need reinforcing - sometimes they need a section of the neck replacing to make them strong again.
Glue and refinish from £80
Neck Reinforcement from £160
New Section of neck from £200
Truss rod repair or replacement Simple - £80 Taking the neck apart from £200Replacement Components
Replacement neck - Bolt-on-Neck £350
Glue-in-Neck - Les Paul style £420
Replacement body £300 for a bolt-on-neck body
Scratch Plate Production
Carbon copies or something unique, we can produce scratch plates in-house to any design.
Typically strat styles from £50 Small sized from £35
Large-Sized or Specialist materials - Mirrored, bakelite, Perspex and Aluminium from £50
Body Routs
Need to make room for an extra pickup or modify a cavity to fit a new switching to your instrument or even adding a tremolo? If some routing needs doing we can help. From £40
Electronics
From the simple, fixing of a loose jack, to custom circuits, we can do everything you would need.
Pickup Installation from £30 Strat £40 hollow bodies £70
Custom switching options £30
Acoustic PCB fixing £30
Pickup Builds and RewindsIn-house pickup winding machine and choice of wires so I can rewind, remake or even create a unique pickup for your instrument.
Rewinds from £40
Pickup Standard Builds £60
Bespoke building £100
Potting service is also available at £30 for unit one reductions are offered on additional units.
Acoustic Specific Repairs
Neck Removal and realignment £60
Loose Bracing
Neck reset
Split sides on an acoustic guitar requiring cleats
Top lifting
Hardware issues
Singular machine head causing issues or the bridge simply does not work anymore, we can offer replacement and upgrades to the hardware of your instrument.
Contact Us
Feel free to get in touch with your details, whether it be a repair, build or question, we'll get back to you to shortly to discuss your requirements.
Philip Porter Guitars © 2024